
Wood is possibly the most common material used for tool handles, but in order to be used properly, it has to be stabilized. Since wood is an organic material, it is sensitive to moisture and temperature, which can make it contract or expand. If that happens, your handle can suffer serious damage and make the knife unsafe to use.
To stabilize wood to make it suitable for knife handles, it must be dried to remove all moisture, have all air removed via vacuum chamber, then be saturated with acrylic resin to fill all the holes and gaps in the wood that would absorb water. This process makes it so the wood no longer changes shape with fluctuating humidity.
The acrylic resin stabilization process brings many other benefits to the table as well. It strengthens even softer woods to degrees that make them usable for knives, makes the wood both resistant to rot and simpler to work with, gives them a great polish, and makes it so they don’t have to be finished, all without compromising the sensation of wood in your hand.
Now, that all sounds well and good, but that brief explanation above probably isn’t enough to tell you how to actually carry out the acrylic resin stabilization process. Don’t worry, while the process certainly sounds complicated on the surface, it’s not as hard as all that. We’ll cover all the steps in detail down below.
Step 1: Gathering all the Materials
Before doing anything in the workshop, you have to make sure you’ve got everything you’ll need to complete the task in mind. The materials you’ll need for stabilizing wood include all of the following:
- Wood: This may seem obvious, but not as much as you think. Not all wood is created equal, and some don’t take to stabilization well. This includes extremely oily woods such as teak and rosewood. Particularly dense woods that don’t allow the resin to penetrate very well are bad choices too. On that front, we don’t recommend anything denser than hard maple.
- Stabilizing Resin: There are many options available in stores, but a heat-activated, pre-catalyzed acrylic resin is best. Using knockoff solutions (acetone with dissolved plexiglass is the most notorious) can damage a vacuum pump. Whatever is chosen, you’ll require enough stabilizing resin to fill the vacuum pump.
- A Toaster Oven: This is to dry out the wood you choose, as well as cure the resin once it is infused within the wood.
- A Vacuum Pump: This tool is extremely vital to the process, so you should acquire the best vacuum pump possible. A two-stage model would be preferable, such as an electric rotary vane pump. You could also use an HVAC service pump.
- A Vacuum Chamber: These can be built yourself or bought. It just has to be sturdy and capable of fitting your wood pieces in it with room to spare.
- 1 Gallon Sealable Freezer Bags: You’ll need bags that can be sealed in order to let the wood you’re using cool to room temperature after the baking step of the process. It doesn’t have to necessarily be one gallon in size, it just needs to be big enough for the wood you’re using.
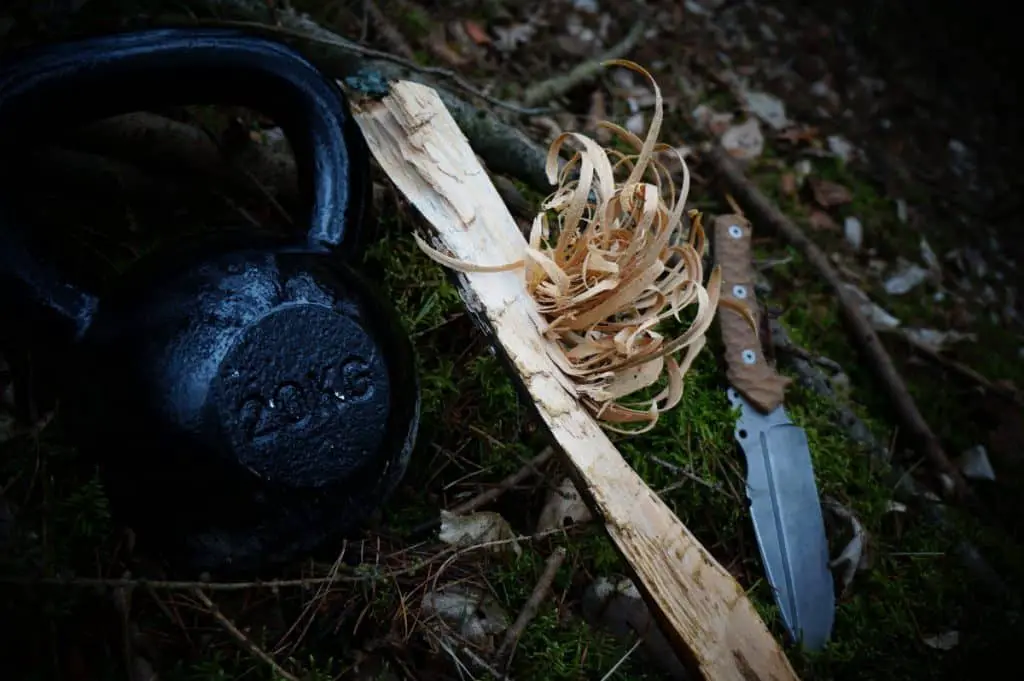
Step 2: Preparing Your Chosen Wood
Drying the Wood
First things first: cut your wood of choice down to sizes that are close to what you actually need. There’s no point in spending time and resources stabilizing a massive chunk of wood, only to use a small chunk of it.
Ideally, you should cut your wood down to just slightly larger than what you need: if all goes well, you can shave off the remainder, but if something does go wrong, you have some breathing room to work with.
Once that is done, the wood must be dried as much as humanly possible. The less moisture is in the wood, the better it will absorb the resin, enhancing your final product. This is not moisture you will be able to feel and identify as ‘wet.’ It’s water molecules in the actual cells of the wood itself.
Thankfully, getting rid of that moisture is fairly easy. Put your wood in the toaster oven at 250 degrees Fahrenheit, and leave it, preferably for several hours. There’s no set amount of time wood needs to be baked to lose all of its moisture, mostly because there’s no way to tell when you can’t feel or see the moisture in the first place.
At the minimum, your wood should bake for two hours, but thicker pieces of wood will likely need more time. The longer you leave the wood in, the less moisture there will be, and the better things will go for your final product. Even leaving the wood baking for eight hours wouldn’t be overkill.
Cooling the Wood
When you feel that you have baked the wood long enough, place it in a zip-top gallon freezer bag, and let them cool down to room temperature. If any condensation forms within the bag, the wood is still not dry enough and needs to be baked longer.
The wood must be put in a sealed bag to cool: if they are left in the air, they will absorb moisture from it and negate the drying process you just went through.
It’s worth noting that the wetter the wood, the more likely they are to warp during the drying process. If you are using very wet wood, you may want to leave them as larger pieces, so you have more to work with if a warp forms.
Step 3: Vacuuming
Do not proceed with this step until the wood is at room temperature. The acrylic resin is heat activated, so if the wood is still hot, it will activate the resin prematurely and ruin the stabilization process. Don’t be afraid to wait a long time to be absolutely sure the wood is cool. Once you’re sure, we can begin the actual stabilization process.
With sufficiently dried wood, place the pieces in your vacuum chamber. The pieces need to have enough space around them to allow the resin to reach all sides, as well as weigh them down so they don’t float around during the stabilization.
When the wood is secure, the chamber should be filled with resin to around 15 millimeters above the wood pieces. It is normal for the resin level to drop during the process because it’s being absorbed into the wood. It’s better to have excess resin instead of not enough. The wood can only absorb so much resin, so there’s no harm in having more than it can take.
When everything is ready, close the vacuum chamber and activate it to begin the air evacuation process. The resin will bubble as the air in the wood escapes. If the resin starts to foam up so much that it runs off, allow the air to slowly escape until that foam dissolves. Repeat this as many times as needed.
When there is no more bubbling in the resin, all of the air has been removed from the wood, which is completely saturated. The whole process generally takes about an hour, though this can, of course, varies.
Once the process is done, deactivate the vacuum after closing the valve and let the wood sit. After the wood sits for a time, the pieces can be taken out so that they can be drained. Once drained, you can dab them with cloth or paper towels to clean the surface.
Step 4: Curing (Baking) The Wood
For the next step, preheat an oven to a temperature between 160 degrees and 200 degrees. You can use an oven thermometer to double-check the temperature if needed. Once at the desired temperature, each handle piece needs to be wrapped in aluminium foil and placed with the glossy side facing inward and the matt side outward.
The wood should be in the oven for a minimum of 60 minutes and a maximum of 90 minutes. When removing the wood from the oven, protective gloves should be used. When this process is finished and the wood is stabilized, it will be significantly heavier than it was before. Keep this in mind when balancing the knife you are making.
Optional Step 5: Color Treatment
Naturally, you do not need to color the wood as part of the stabilization process. However, there’s no denying that a wooden handle can greatly benefit from a vivid color. If you do color the wood, a good rule of thumb is to use a coloring agent from the same manufacturer you bought your acrylic resin from.
It’s not that you absolutely have to do that; however, using products from the same manufacturer ensures that there aren’t any unforeseen complications or reactions between incompatible ingredients or chemicals. It’s just better to play it safe, lest you ruin all of your hard work.
If you don’t care to color the wood, then congratulations: you have successfully stabilized a piece of wood that you can safely use for a knife handle.